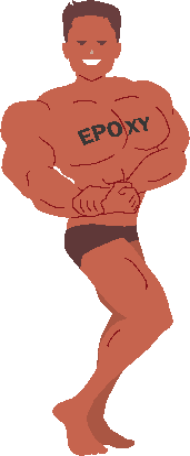
Irreversibly sticky with outstanding adhesive strength and durability: 'Bodybuilders.'
What is an epoxy?
An extremely durable plastic that is cured by heat and light
An epoxy is a type of tough plastic material.
When an epoxy compound is mixed with a curing agent and exposed to heat and light, a chemical reaction occurs, causing molecules to be linked three-dimensionally to form a durable hardened body. This hardened body is extremely tough and chemically stable. It also has excellent properties, such as high adhesive strength, durability, and electrical insulation. Thus, it is used for various usages.
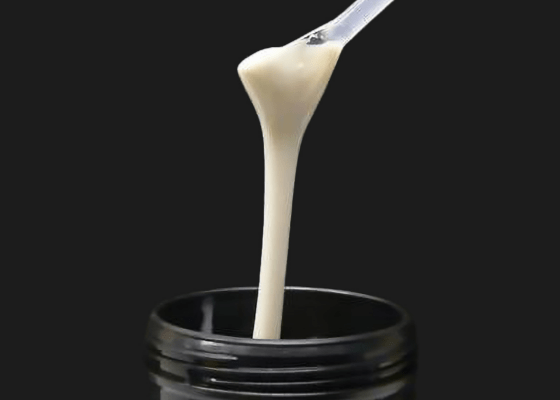
Familiar products in which epoxies are used
Epoxies used in adhesives, paints, and electronic materials
Epoxies are used in adhesives, coatings, paints for vehicles and vessels, etc., civil engineering and construction materials, parts for electronic devices, such as TV sets, smartphones, and PCs, etc. They are used in many products around us and support our daily lives.
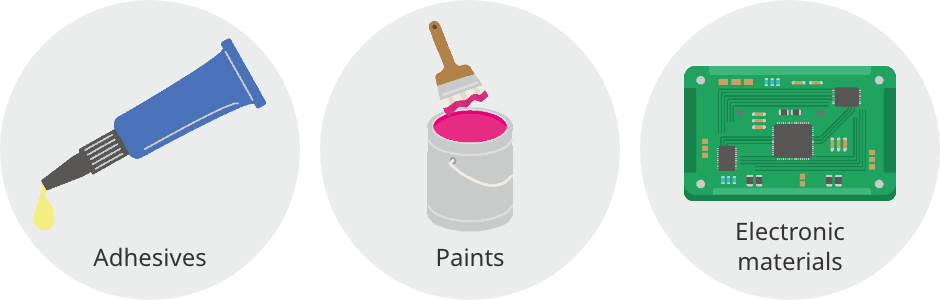
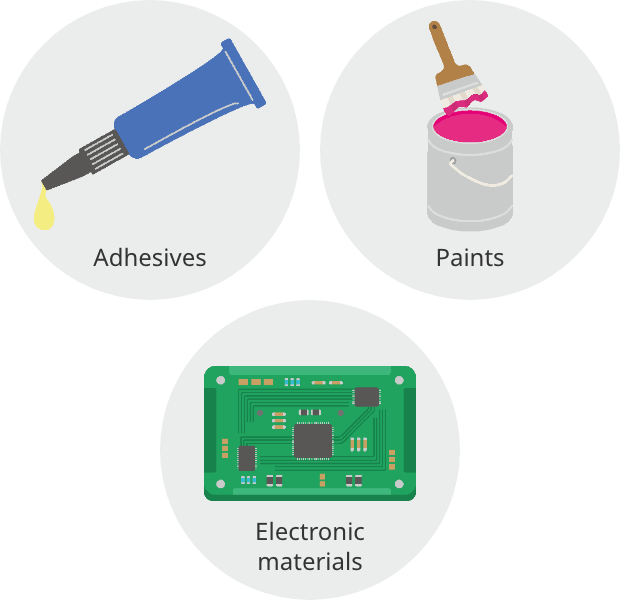
Epoxies are similar to bodybuilders.
Bodybuilders train their bodies to build strong muscles. Their muscles are extremely strong and durable and immune to impact to some extent.
Similarly, epoxies form tough structures by bonding molecules through a chemical reaction. The structures are extremely stable and durable and therefore can withstand various environmental changes and severe conditions.
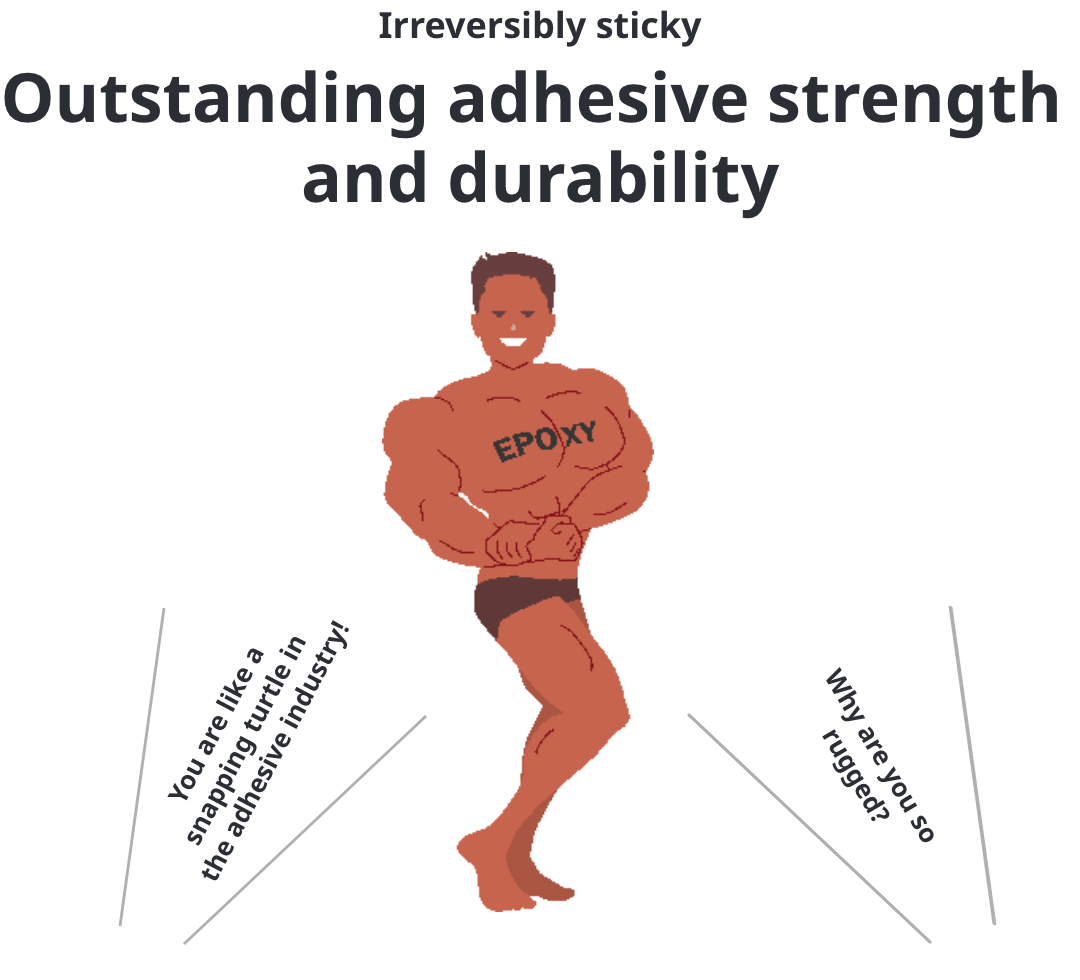
11 main features
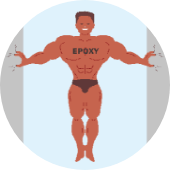
Adhesive strength and mechanical strength
Adhesive strength that makes it impossible to remove once stuck
Once a bodybuilder exerts force to grip an item, it is difficult to remove the item. A bodybuilder also has a strong body that does not break when subjected to any impact. Epoxies form extremely strong chemical bonds when cured. This makes it possible to exhibit high adhesive strength and mechanical strength.
Why do epoxies have outstanding adhesive strength?
Because molecules are linked three-dimensionally.
The high adhesive strength of epoxies is attributed to the three-dimensional molecular structures. Epoxies strongly adhere to the surface of a material and form a three-dimensional network (three-dimensional crosslinking) through a chemical reaction. Because this network is extremely strong, adhesives demonstrate excellent features.
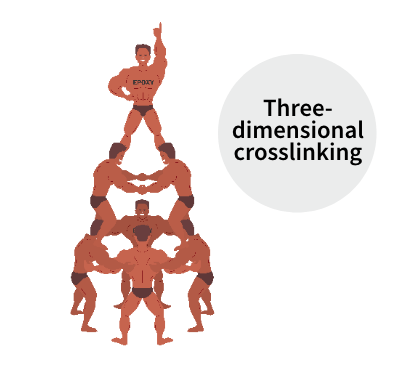
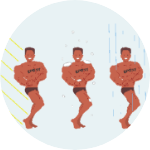
Long-term durability
No deterioration even in severe environments over the long term
Once bodybuilders strikes a pose, they become immovable no matter what.
Epoxies do not deteriorate even when exposed to high temperature, low temperature, or high humidity environments. Because epoxies are chemically stable, they demonstrate high durability against external stress and environmental changes and maintain high performance over the long term.
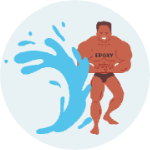
Water resistance, moisture resistance, and chemical resistance
No deterioration even when exposed to water, moisture, or chemicals
The durable body of bodybuilders remains unaffected even when exposed to water, moisture, or chemicals.
Epoxies remain unaffected even when exposed to water, humid environments, or chemicals, retaining high strength and stability.
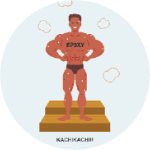
Heat curing
Cured when heated
Bodybuilders build strong bodies by raising their body temperature and promoting heat generation in their muscles through training.
Epoxies are cured when heated, forming a hardened body characterized by high strength and durability.
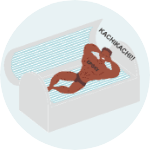
Photo-curing
Cured when exposed to light
Some bodybuilders darken their skin by exposing themselves to ultraviolet rays.
Some epoxies are cured when exposed to light, including ultraviolet rays. Photo-curing epoxies have properties to be cured through a chemical reaction when exposed to light of specific wavelengths.
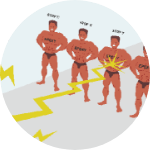
Electrical insulation
Nonelectroconductive
The well-trained, robust muscles of bodybuilders do not conduct electricity.
Epoxies are characterized by high electrical insulation and have properties to prevent the conduction of electricity. High electrical insulation plays a key role in situations where electrical insulation is required for electronic parts.
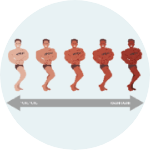
Hardness and color variations
Freely adjustable hardness and color
Epoxies are available in a wide variety. Adjustments can be made in a wide range from soft and flexible materials to extremely hard materials.
The color can also be controlled freely, including clear, white, and black.
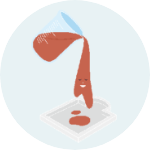
Low viscosity/
easy workability
Liquid and easy to process before curing
Before they are cured, most epoxies are liquid or apparently solid but liquefy when heated, etc. Thus, they can be applied neatly even in narrow spaces or can be formed.
Once cured, they become solid and form a tough structure.
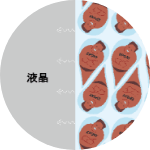
Low contamination
No leaching of unnecessary components when cured
Epoxies are used as adhesives when assembling liquid crystal displays.
When epoxies are cured, their components hardly leach. Thus, even if liquid epoxies before curing come into contact with liquid crystals, they do not leach into liquid crystals. Such properties ensure the high display quality of liquid crystal displays.
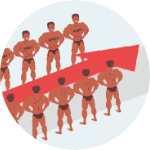
Low insertion loss
Preventing signal loss by creating a path for high frequencies
When signals used for electronic devices and communication are transmitted, they may become slower or weaker. This is called insertion loss. Notably, insertion loss tends to increase for high-frequency signals.
Epoxies can suppress insertion loss depending on their design. They are suitable for components for high-speed data communication and information transmission in which high-frequency signals are used.
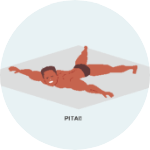
Low warpage
Minimal tendency to warp when spread thinly
Epoxies are strong and highly rigid and characterized by minimal warpage.
They are resistant to deformation when subjected to heat and physical stress, etc. and can maintain a stable shape. Thus, epoxies are highly reliable materials in various usages.
Applications of epoxies
Adhesives for assembling liquid crystal panels
Epoxies are used as adhesives to assemble liquid crystal panels (sealing materials for liquid crystals). The use of these adhesives makes it possible to manufacture liquid crystal panels in a short time, helping to shorten the process.
Our sealing materials for liquid crystals hardly leach into liquid crystals, achieving excellent display quality.
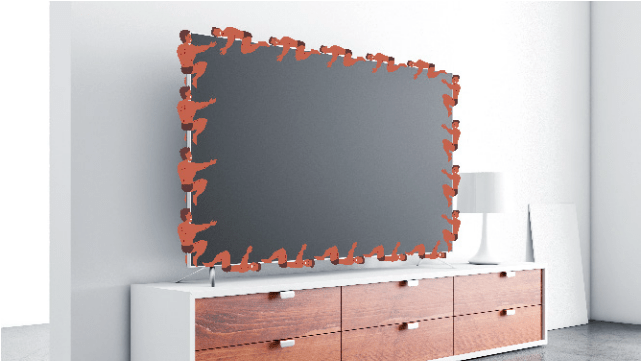
Features
Adhesive strength and mechanical strength
Low viscosity/easy workability
Low contamination
Moisture-proof sealant for organic EL displays
Epoxies are also used in organic EL panels. They can protect devices of organic EL displays from moisture and external environments and offer high reliability.
Our proprietary optically post curable system enables bonding of UV-blocking materials or UV- and heat-sensitive surfaces.
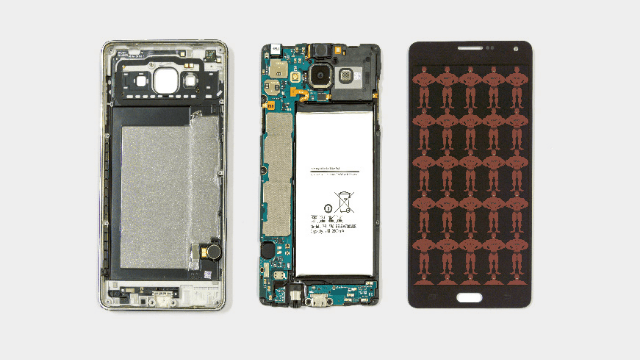
Features
Photo-curing
Water resistance, moisture resistance, and chemical resistance
Interlayer dielectric films for semiconductor package substrates
An interlayer dielectric film is used to form microwiring on semiconductor package substrates. It is nonelectroconductive and prevents mutual interference.
It is essential to ensure low insertion loss in high-speed communication and warpage control of thin-film substrates. Our materials have superb properties.
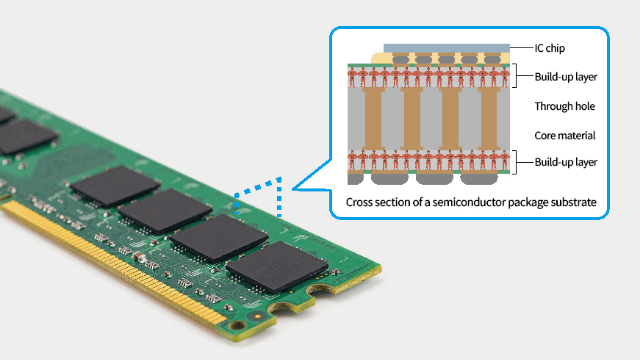
Features
Electrical insulation
Low insertion loss
Low warpage
Insulating and adhesive heat release sheets for power devices
An insulating and adhesive heat release sheet transfers heat in an electronic device to the outside to prevent overheating of the device.
Characterized by high thermal conductivity and electrical insulation, our materials prevent performance deterioration and failure of electronic devices, thereby achieving high reliability.
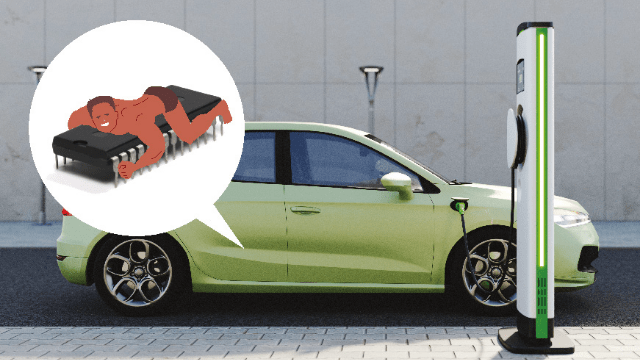
Features
Electrical insulation
Long-term durability
Introduction of products
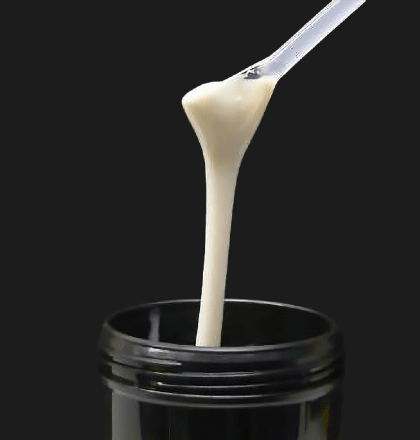
Photolec™ S
ODF sealant for LCDs (an adhesive for assembling liquid crystal panels)
Adherent body(Adhesive): Glass, Polyimide
Curing conditions: UV (3,000mJ / cm2) + Heat (120°C × 60min)
Features
- Helps prevent display defects of liquid crystal panels
- Easy to handle and dispense with a narrow width
- Excellent adhesion even to non-metallic materials, such as alignment films
Process
Sealing materials for liquid crystals are a type of adhesive used for manufacture of liquid crystal panels. In the One Drop Fill (ODF) method, which is one of the methods to manufacture liquid crystal panels, liquid crystals are dispensed concurrently with bonding of the upper and lower substrates using a sealing material for liquid crystals in a vacuum, enabling quick manufacturing.
Our sealing materials for liquid crystals can be used for the ODF method and contribute to shortening the manufacturing process. Because they hardly leach into liquid crystals, excellent display quality can be realized.

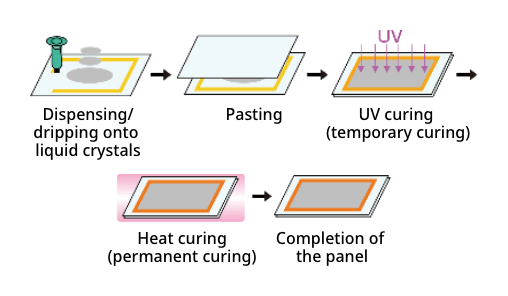
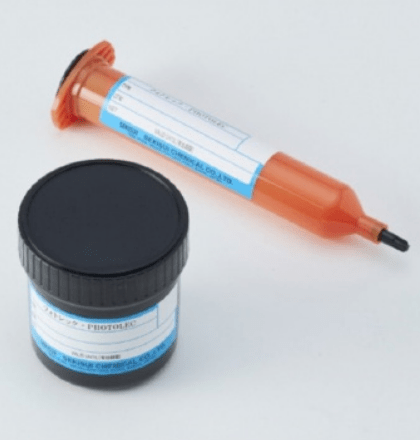
Photolec™ E
UV delayed curing low-moisture-permeable adhesive
Adherent body(Adhesive) : Alkali free glass
Curing conditions: UV delayed (UV 1,500 mJ/cm2) + Heat (60 - 100°C × 30 min)
Features
- Curing starts a few minutes after UV exposure. Subsequent low-temperature heating for a short time completes curing quickly.
- Functions, including low outgassing and water vapor barrier performance, are imparted.
Application to processes in which UV exposure cannot be performed
Photolec™ E is a UV delayed adhesive that can also be applied to UV-impermeable materials and UV-sensitive surfaces.
With its delayed curing feature (adjustable from 5 to 20 minutes) instead of immediate curing after UV exposure, Photolec™ E can also be used for processes that cannot be performed by immediate curing after UV exposure. The low-moisture-permeable, contamination-resistant resin prevents contamination from external factors or ingress of moisture. There may be some processes that cannot be performed by UV exposure, such as processes to mount camera modules and bond organic EL displays (OLEDs). Ingress of moisture from the bonding area, which can cause defects, must be prevented. Notably, OLED panels require high optical performance.
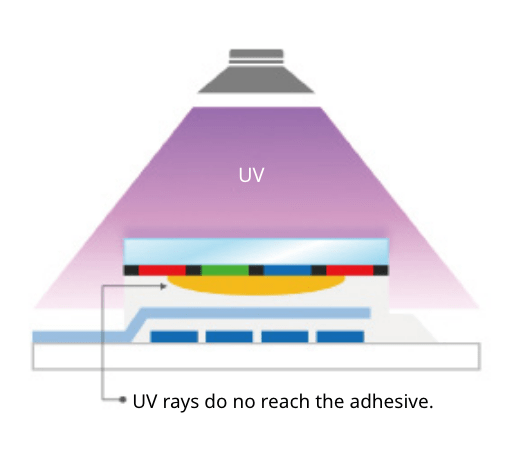
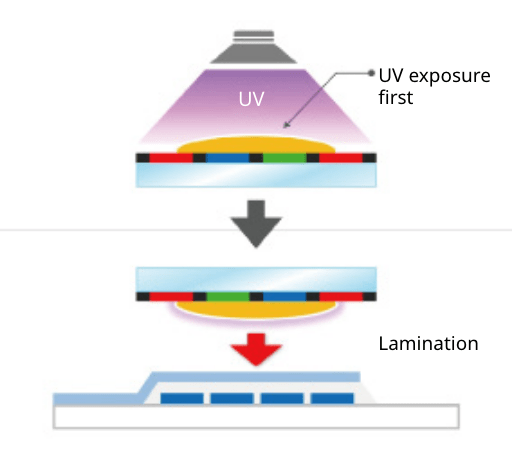
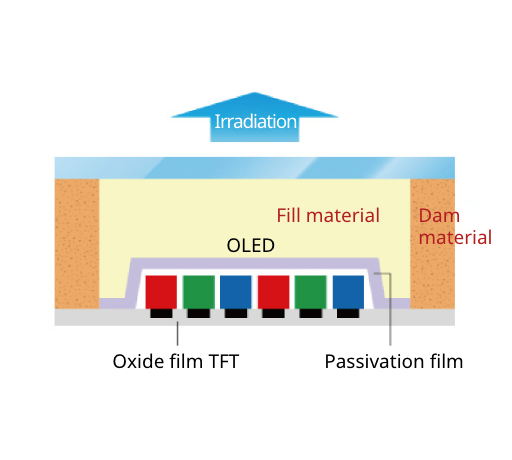
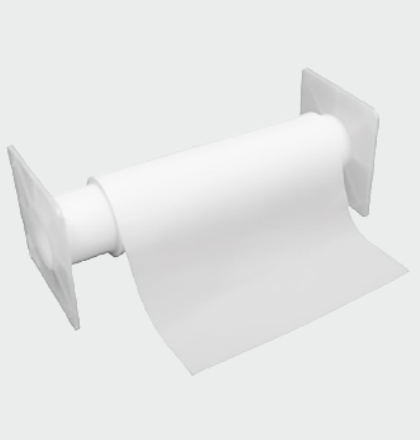
Build-up Dielectric Films
Interlayer dielectric films for semiconductor package substrates
Features
- Achieve low insertion loss and enable warpage control
- Have a track record in high-layer-count/large-sized high-end IC package substrates
- Contribute to higher flexibility in package designs with high reliability
What is a Build-up Dielectric Film?
The Build-up Dielectric Films are interlayer dielectric films used for forming microwiring on IC package substrates. Interlayer dielectric films are nonelectroconductive and prevent mutual interference of different circuits and parts. In line with the advancement of microwiring and high-speed communication of electronic devices, the Build-up Dielectric Films are required to minimize the insertion loss.
In line with the need for thin films for devices, the films are required to minimize the warpage of thin substrates. Our materials have excellent characteristics for the above properties.
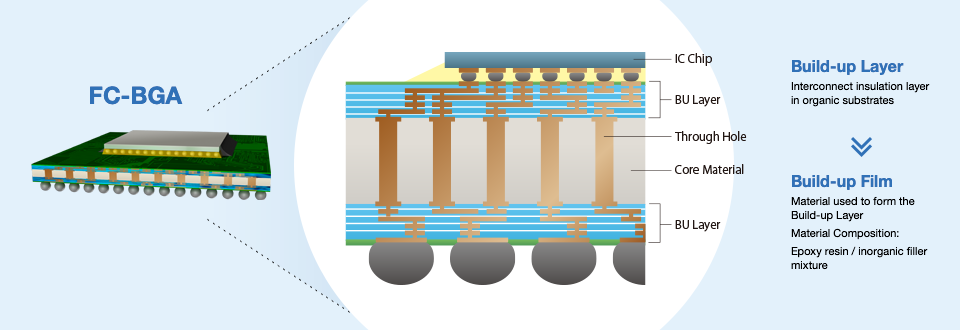
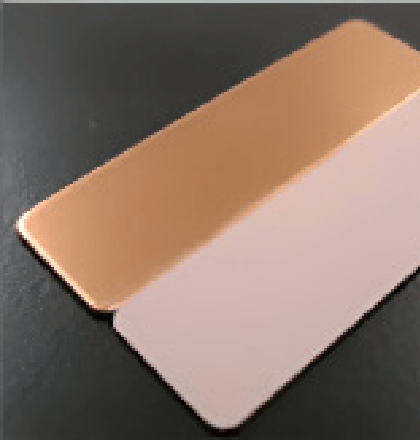
Insulating and adhesive heat release sheets
These heat release materials can be applied to power devices, etc. Both high thermal conductivity and high electrical insulation are realized by high density packing of fillers with excellent thermal conductivity.
Features
- Heat release materials characterized by high thermal conductivity and excellent electrical insulation
- Excellent heat resistance, high adhesiveness, and high reliability
Applications and usages
The substrates have an adhesive (heat-curing) insulation layer in the B-stage condition.
Application to a wide range of materials : It is possible to combine them with various kinds of materials of diverse thicknesses due to excellent sheet properties and adhesiveness. Please consult us for integration with workpieces in different forms, such as those with uneven or rough surfaces.
Stable adhesion : They have an extremely smooth adhesive surface, enabling stable temporary mounting to workpieces in typical conditions.
Special processing technology/quality control technology : They exhibit stable performance due to quality control technology based on many years of experience.
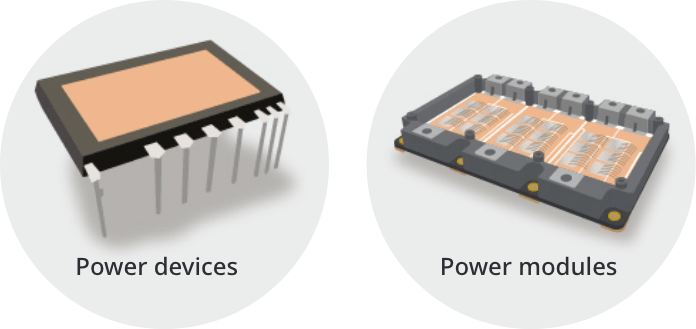
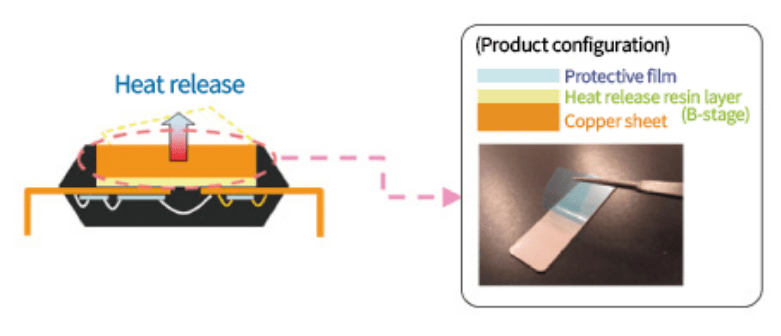